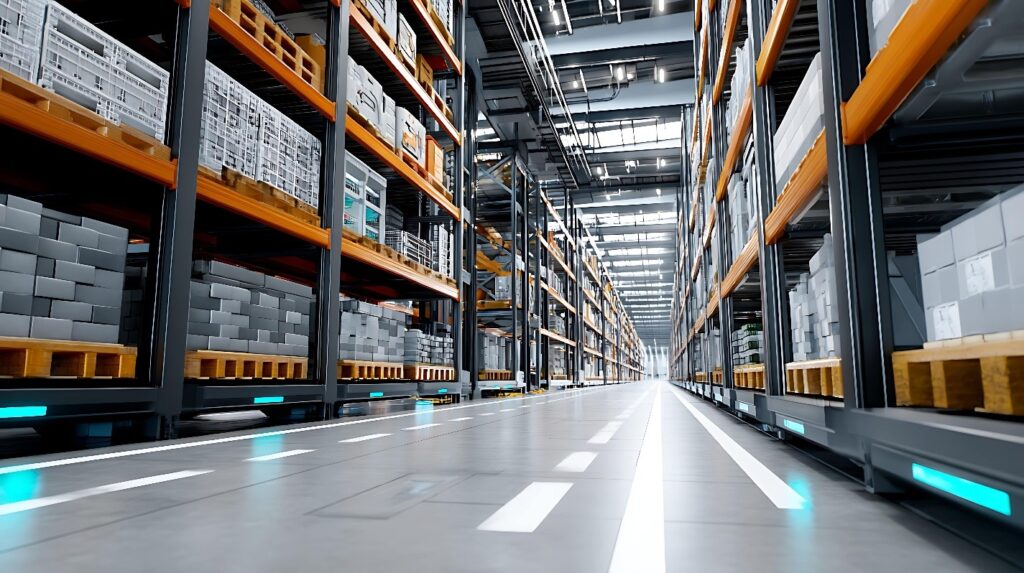
In today’s fast-paced workplaces, storage solutions need to do more than just hold supplies—they must support productivity, improve accessibility, and adapt to changing needs. That’s where mobile shelving comes in. These versatile units combine the structural capacity of traditional shelving with the convenience of mobility, allowing users to bring supplies directly to the point of need.
Global Industrial reviews how whether in healthcare, warehousing, manufacturing, or retail, mobile shelving helps create organized, efficient, and dynamic environments. Instead of confining storage to specific corners of a facility, these systems travel wherever they’re needed, ensuring that tools, inventory, or materials are always close at hand.
What Is Mobile Shelving?
Mobile shelving systems are essentially storage units mounted on wheels or casters, designed to be easily moved around a space. Unlike conventional stationary shelves, which require workers to walk back and forth to access stored items, mobile shelves bring the storage to the workers. This mobility not only enhances convenience but also supports a more ergonomic and efficient workflow.
Unlike high-density shelving that compresses stationary racks along a track system, mobile shelving is free-moving and untethered. These systems often function as utility carts or even transport trolleys, offering flexible usage across a variety of applications. Depending on their construction, they can include adjustable shelves, locking doors, collapsible structures, or multi-access sides.
Key Benefits of Mobile Shelving
Mobile shelving is more than just a practical upgrade—it’s a strategic tool for streamlining operations and enhancing workplace functionality. Below are some of the most impactful advantages these systems provide:
1. Customizable to Meet Unique Needs
No two workspaces are exactly alike. Mobile shelving units are designed with flexibility in mind, offering adjustable shelves, various compartment configurations, fold-down sides, and lockable doors. This adaptability allows businesses to tailor their storage setups based on specific inventory types, workflow requirements, or space limitations.
2. Enhanced Accessibility
With mobile shelving, supplies don’t remain locked in a backroom. Instead, they travel with the team, ensuring immediate access at workstations, operating rooms, retail floors, or construction sites. This reduces the need for unnecessary walking and minimizes disruptions during tasks.
3. Improved Organization
A cluttered space hinders productivity. Mobile shelving makes it easier to implement a structured system where each item has its place. With modular features, inventory can be categorized, labeled, and sorted for quick retrieval, supporting a tidy and professional environment.
4. Increased Operational Efficiency
Lost time adds up fast—especially when employees are constantly searching for tools or parts. By making storage portable, mobile shelving shortens the time spent on retrievals, reduces downtime, and helps maintain momentum throughout the workday.
5. Access From Multiple Angles
Many mobile shelving systems are designed for 360-degree access, allowing users to load and unload from multiple sides. This is particularly helpful in fast-moving environments where speed and flexibility are essential, such as fulfillment centers or emergency response operations.
6. Built for Durability
From heavy-gauge steel frames to industrial-strength casters, mobile shelving systems are engineered to withstand the demands of high-use environments. Whether storing tools, medical supplies, or retail stock, these shelves offer long-lasting performance even under rigorous conditions.
7. Adaptable for the Future
Business needs evolve, and so should your storage. The modular nature of mobile shelving means units can be adjusted or reconfigured over time—expanding with inventory growth, accommodating new equipment, or transitioning between departments.
Popular Mobile Shelving Configurations
Mobile shelving is not one-size-fits-all. Various designs and materials cater to different industries and usage conditions:
• Wire Shelf Trucks
Lightweight yet strong, wire shelf units are great for both dry and humid environments. Their open design promotes airflow and visibility, making them ideal for food service, laboratories, and clinical settings. Chrome, epoxy, and zinc-coated options offer varying levels of corrosion resistance.
• Plastic Shelf Carts
Made from rust-proof, easy-to-clean polymers, plastic shelving units are often chosen for their antimicrobial properties and lightweight build. They’re well-suited to healthcare environments, sterile storage areas, or any setting where hygiene is a top priority.
• Steel Shelf Units
When durability is non-negotiable, steel shelving provides unmatched strength. These units can support heavy loads and are frequently used in auto shops, manufacturing plants, and large warehouses where reliability under pressure is key.
• Security Carts
For valuable or sensitive inventory, enclosed mobile shelving with lockable wire mesh doors adds an extra layer of protection. These carts provide visibility of contents while preventing unauthorized access—a common choice for electronics, pharmaceuticals, and retail goods.
Choosing the Right Casters
The performance of a mobile shelving system depends heavily on its casters. Choosing the wrong type can affect maneuverability, safety, and shelf longevity. Here are some common caster types to consider:
- Soft Casters – Ideal for smooth indoor surfaces like office floors or hospitals.
- Heavy-Duty Casters – Engineered to withstand the demands of industrial environments and handle significant weight.
- Outdoor Casters – Designed for uneven surfaces or outdoor use, ensuring smooth mobility in more rugged areas like loading docks or construction zones.
Casters come in swivel and rigid styles, and some models include braking mechanisms to lock shelves in place when stationary.
Making the Most of Mobile Storage
Implementing mobile shelving isn’t just about adding wheels to your storage. It’s about rethinking how supplies, materials, and tools move through your facility. By adopting a mobile-first storage strategy, businesses can enhance worker productivity, reduce clutter, and respond more fluidly to operational changes.
Whether supporting hospital staff with movable medical carts, equipping warehouse workers with portable shelving, or giving retail employees faster access to stock, mobile shelving adapts to your workflow rather than forcing your workflow to adapt to it.
In an era where efficiency and adaptability are paramount, mobile shelving solutions offer a powerful upgrade to traditional storage. These systems bring storage to the action, improve accessibility, and support an agile, well-organized workspace. By investing in mobility, businesses gain not just a new shelving solution—but a smarter, more responsive way to work.